Understanding the Importance of an OEM CNC Lathe Turning Parts Factory
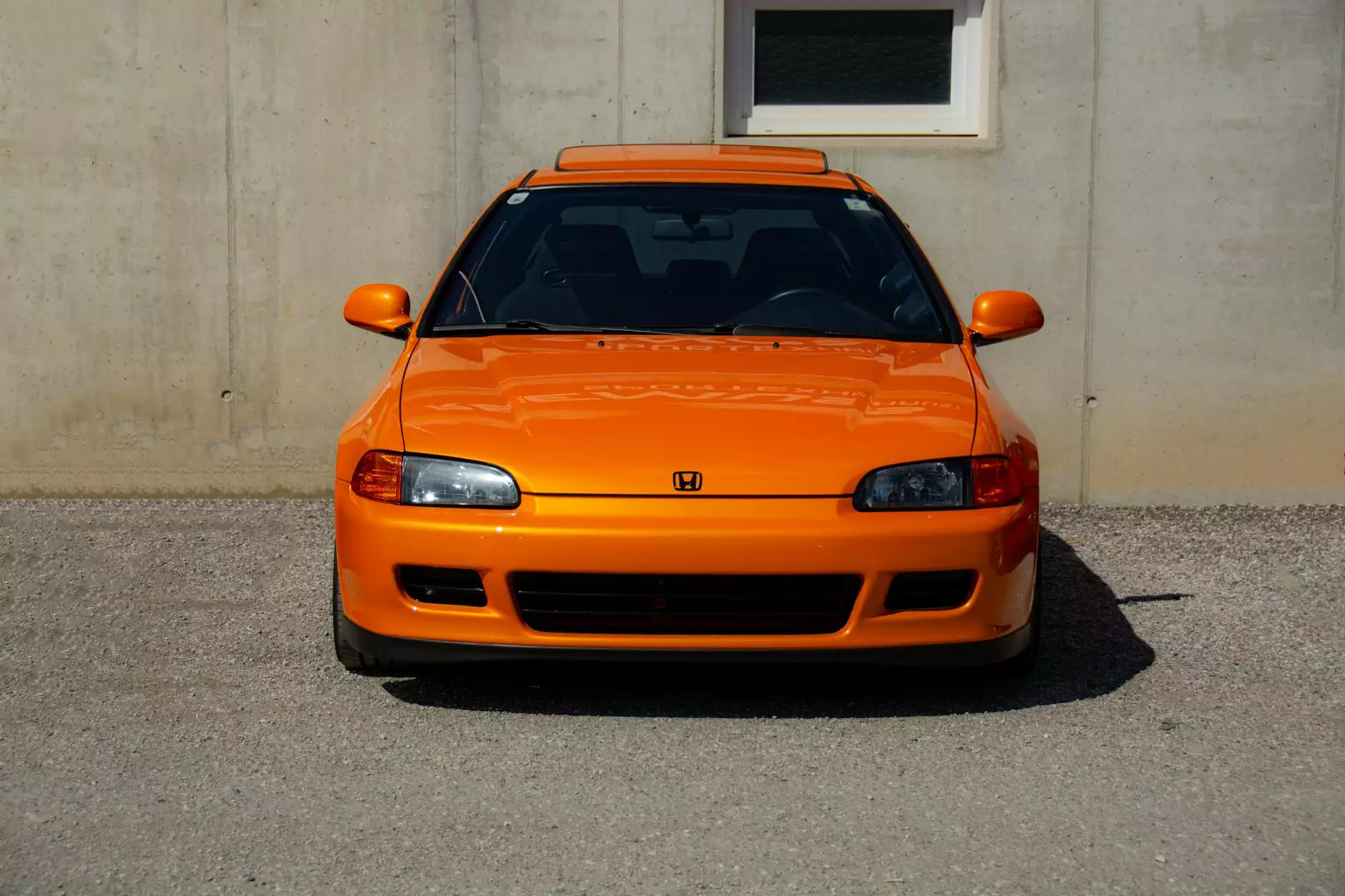
In today's competitive industrial landscape, the demand for precision and quality in manufacturing is at an all-time high. Companies are constantly seeking ways to improve their production efficiency and ensure that their products meet the highest quality standards. One of the critical components to achieving this goal is partnering with an OEM CNC lathe turning parts factory. This article explores why choosing the right factory for your CNC turning parts is essential and how it can significantly benefit your business.
What is OEM CNC Lathe Turning?
Before delving into the benefits of selecting an OEM CNC lathe turning parts factory, it’s essential to understand what OEM and CNC lathe turning mean.
- OEM (Original Equipment Manufacturer): This refers to a company that produces parts or equipment that may be marketed by another manufacturer. These are typically high-quality parts that are built to exact specifications.
- CNC (Computer Numerical Control) Lathe Turning: This is a manufacturing process that involves the automatic control of machining tools using a computer. It allows for precise shaping and cutting of materials, resulting in high-quality components.
Why Choose an OEM CNC Lathe Turning Parts Factory?
The decision to work with an OEM CNC lathe turning parts factory can profoundly impact your manufacturing efficiency, cost-effectiveness, and product quality. Here are some of the advantages:
1. Precision Engineering and Quality Assurance
One of the primary advantages of working with an OEM CNC lathe turning parts factory is the guarantee of precision engineering. CNC machines are designed to produce parts with a high degree of accuracy, minimizing the risk of human error common in manual machining processes. This precision ensures that every component meets the required specifications, providing reliability and consistency in production.
2. Access to Advanced Technology
OEM factories invest heavily in the latest technologies and machines. They employ advanced CNC turning equipment that improves the production process's efficiency and quality. These technologies include:
- Multi-axis CNC machines: These machines can perform complex operations that allow for more intricate component designs.
- Robotics and automation: These technologies help streamline processes, reduce labor costs, and improve turnaround times.
- Real-time quality control systems: These systems ensure that each part produced meets quality standards before it leaves the factory.
3. Customization and Flexibility
Partnering with an OEM CNC lathe turning parts factory allows businesses to customize their orders to suit specific needs. Whether you require unique dimensions, materials, or finishes, OEM manufacturers can accommodate these requests without compromising quality. This customization capability is invaluable, particularly for industries that require specialized components.
4. Cost-Effectiveness
While some might assume that working with an OEM CNC lathe turning parts factory is more expensive, the reality is often the opposite. The efficiency gained from using advanced CNC machinery can lead to reduced labor and operational costs. Furthermore, the precision of CNC machining reduces material waste, ultimately leading to lower production costs over time. Businesses can scale their production without incurring significant additional costs.
The Role of Quality Control in OEM CNC Lathe Turning
Quality control is a fundamental aspect of any reputable OEM CNC lathe turning parts factory. Quality assurance processes assess materials, production methods, and finished products to ensure they meet industry standards. Effective quality control measures include:
- Incoming material inspection: Ensuring that all materials used in the production process meet specified quality standards.
- In-process inspection: Regularly checking parts during production to identify defects early and prevent compromised components from reaching the final stage.
- Final product inspection: Conducting thorough evaluations of finished products to ensure they meet specifications before shipping.
Industries Benefiting from OEM CNC Lathe Turning Parts
Many industries benefit from the capabilities of an OEM CNC lathe turning parts factory. Some key sectors include:
1. Aerospace and Defense
The aerospace industry requires parts that meet stringent safety and performance standards. Precision lathe turned components are crucial for aircraft engines, structural elements, and more. Partnering with an OEM manufacturer ensures that components are produced with the utmost quality and reliability.
2. Automotive
In the automotive sector, manufacturers require a vast array of precision parts, from engine components to transmission systems. OEM CNC lathe turning allows for high volumes of consistently high-quality parts that meet regulatory requirements.
3. Medical Devices
Medical device manufacturing often requires components made from biocompatible materials and designed to meet rigorous health regulations. OEM CNC turning can produce intricate parts with precision, critical for devices like surgical instruments and implants.
4. Electronics
The electronics industry relies on precision components for devices ranging from smartphones to complex machinery. CNC lathe turning allows for the efficient production of small yet complex parts essential for modern electronics.
Choosing the Right OEM CNC Lathe Turning Parts Factory
Selecting the right factory to partner with is a crucial decision that can influence your product quality and production timelines. Here are some key factors to consider:
- Experience and Expertise: Look for factories with extensive experience in CNC lathe turning and a proven track record of delivering quality products.
- Capabilities and Technology: Ensure the factory is equipped with advanced CNC machinery that can handle the complexity of your parts.
- Quality Certifications: Check for industry-standard certifications that indicate the factory's commitment to quality, such as ISO 9001.
- Customer Support: A reliable factory will offer excellent customer support, providing clear communication and assistance throughout the manufacturing process.
Future Trends in CNC Turning
As industries continue to evolve, so does technology within the manufacturing sector. Here are some emerging trends that could shape the future of OEM CNC lathe turning:
1. Automation and AI Integration
The incorporation of artificial intelligence in CNC machinery is set to enhance the precision and efficiency of production processes even further. Automated systems can learn from past production runs to optimize machining strategies, reducing cycle times and improving output quality.
2. Sustainable Manufacturing
With the growing emphasis on sustainability, many manufacturers are seeking ways to reduce waste and energy consumption. OEM CNC lathe turning parts factories are expected to adopt eco-friendly practices, including recycling materials and using energy-efficient machinery.
3. Enhanced Customization through Software
Advancements in software will enable more intricate customization options, allowing clients to specify not just dimensions but also design features that can be rapidly prototyped. This flexibility will cater to an increasingly diverse range of customer needs.
Conclusion
In conclusion, partnering with a reputable OEM CNC lathe turning parts factory presents numerous advantages for businesses in various industries. From ensuring the quality and precision of parts to providing customization options and enhancing cost-effectiveness, the benefits are clear. As technology advances, the role of OEM manufacturers will only continue to grow, making them an essential part of successful modern manufacturing.
As you consider your manufacturing needs, remember to evaluate potential partners based on their experience, technology, and commitment to quality. Choosing the right OEM factory can be a game-changer for your business, positioning you for long-term success in an ever-evolving marketplace.