Understanding Die Casting Manufacturing
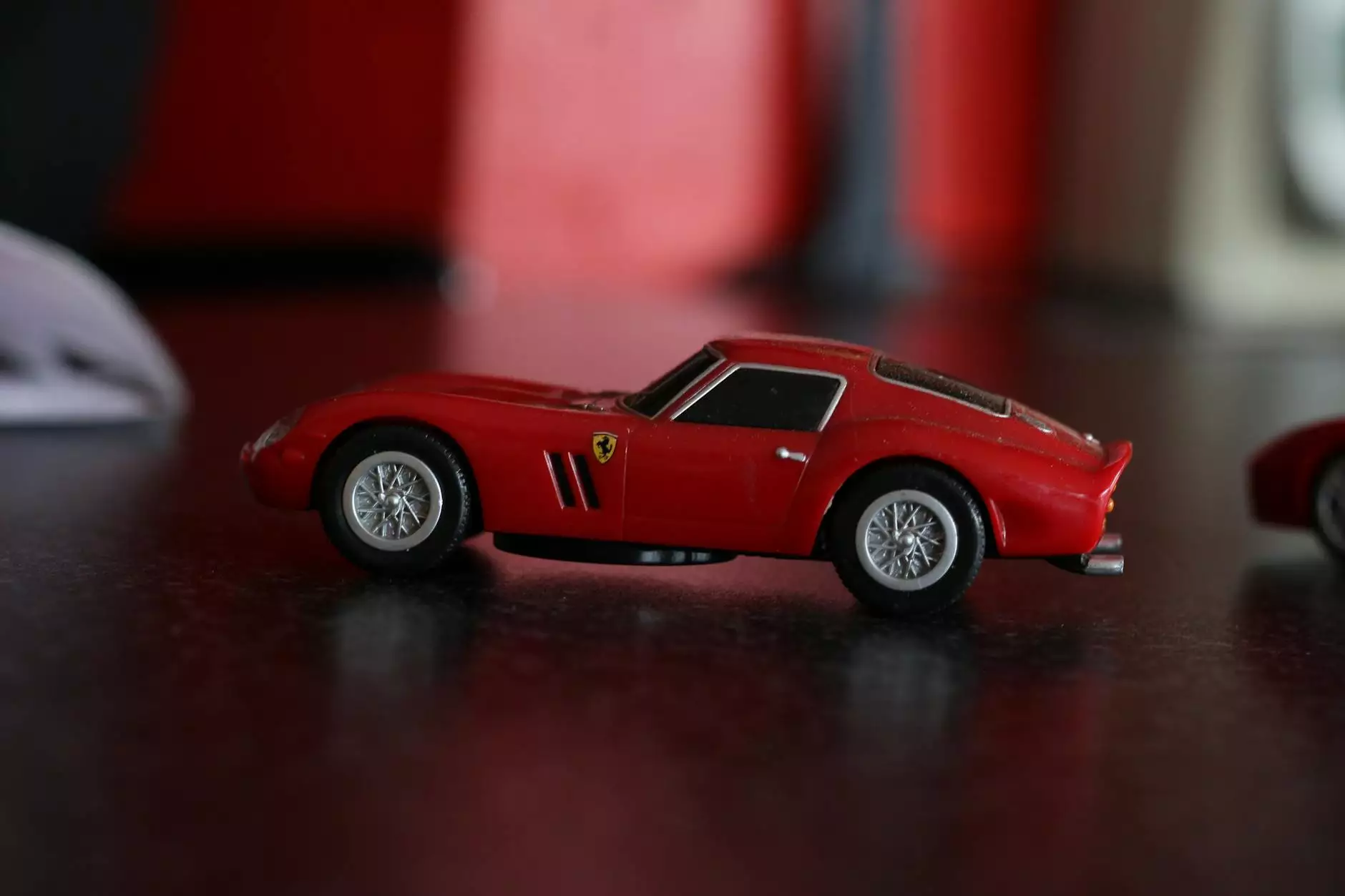
In today’s competitive industrial landscape, the significance of efficient manufacturing processes cannot be overstated. Among these processes, die casting manufacturing stands out as a pivotal method in metal fabrication. This article delves into what die casting is, its benefits, applications, and the key factors that one should consider while choosing a die casting manufacturer.
What is Die Casting?
Die casting is a versatile metal forming process that involves forcing molten metal into a mold cavity under high pressure. This method allows for the production of complex shapes with high precision and a smooth finish.
Types of Die Casting Processes
There are primarily two types of die casting processes:
- High-Pressure Die Casting: In this process, molten metal is injected into a steel mold under high pressure, which solidifies quickly. It is ideal for mass production of small to medium-sized products.
- Low-Pressure Die Casting: Here, a low-pressure system is used to fill the mold. This method is suitable for larger parts which require a uniform wall thickness.
Advantages of Die Casting Manufacturing
Choosing the die casting manufacturing process offers numerous advantages for businesses looking to streamline their production while maintaining high quality.
1. High Precision and Repeatability
Die casting provides exceptional dimensional accuracy, ensuring that each piece produced meets exact specifications. This level of precision is particularly beneficial in industries where tight tolerances are essential.
2. Efficient Production Rates
Due to the rapid solidification of metal, die casting can produce a large volume of parts in a shorter amount of time compared to other metalworking methods. This efficiency results in reduced labor and manufacturing costs, making it an attractive option for large-scale production runs.
3. Excellent Surface Finish
The smooth surface finish of die cast parts often requires little to no additional machining, reducing the overall time and cost of the production process.
4. Design Flexibility
With the ability to create complex shapes and geometries, die casting manufacturers can accommodate many design specifications. This flexibility allows for innovative designs that can enhance product functionality.
5. Material Versatility
Die casting is compatible with a variety of metals, including:
- Aluminum
- Zinc
- Magnesium
- Brass
This variety allows manufacturers to select the most suitable material based on the desired mechanical properties and application requirements.
Applications of Die Casting
The applications of die casting span across various industries due to its versatility. Here are some notable fields where die casting is commonly used:
1. Automotive Industry
The automotive sector relies heavily on die casting for producing components such as engine blocks, transmission cases, and other critical parts due to necessity for durability and lightweight properties.
2. Electronics
Die casting is used to create housings and components for several electronic devices, where heat dissipation, lightweight construction, and efficient assembly are critical.
3. Aerospace
Precision parts required in aerospace applications benefit immensely from die casting due to the stringent safety and performance standards in this field.
4. Industrial Machinery
Industrial machines increasingly utilize die-cast components for robust and efficient functionality, proving the process's adaptability to different sectors.
Choosing the Right Die Casting Manufacturer
Selecting the right die casting manufacturer is crucial to achieving high-quality results. Here are some key factors to consider:
1. Experience and Expertise
It’s vital to choose a manufacturer with a proven track record in die casting. An experienced manufacturer will understand the nuances of the process and be able to offer valuable insights and recommendations.
2. Technology and Capabilities
Investigate the technology and machinery employed by the manufacturer. Advanced automation and up-to-date equipment can significantly affect the quality and efficiency of the die casting process.
3. Quality Control Processes
Reliable manufacturers implement rigorous quality control measures throughout the production process. Look for certifications like ISO 9001, which indicate a commitment to quality management.
4. Customer Service and Support
Strong customer service is essential for effective communication, issue resolution, and timely delivery. Ensure that the manufacturer you choose values customer feedback and support.
5. Flexibility and Customization
Every project is unique. A good die casting manufacturer should offer customization options to cater to specific project needs, ensuring that they can adapt to your requirements.
The Future of Die Casting
The die casting industry is evolving with advancements in technology. New methods, such as:
- 3D Printing for Die Prototypes: This innovation allows for quicker and more efficient prototyping, reducing lead times significantly.
- Improved Alloys: Development of new metal alloys enhances performance capabilities across various applications.
These advancements promise to make die casting even more efficient and versatile in the future.
Conclusion
In conclusion, die casting manufacturing is an integral part of modern metal fabrication that offers numerous benefits, from precision and cost efficiency to design flexibility and speed of production. Industries ranging from automotive to aerospace depend on this method to deliver high-quality components. By partnering with a skilled and experienced die casting manufacturer, businesses can leverage these advantages to stay competitive in their respective markets.
If you’re looking for a trusted partner in die casting, consider reaching out to the experts at DeepMould. With extensive experience and a commitment to quality, they are well-equipped to meet your die casting needs.