Understanding Mold Plastic Injection: A Key to Modern Manufacturing
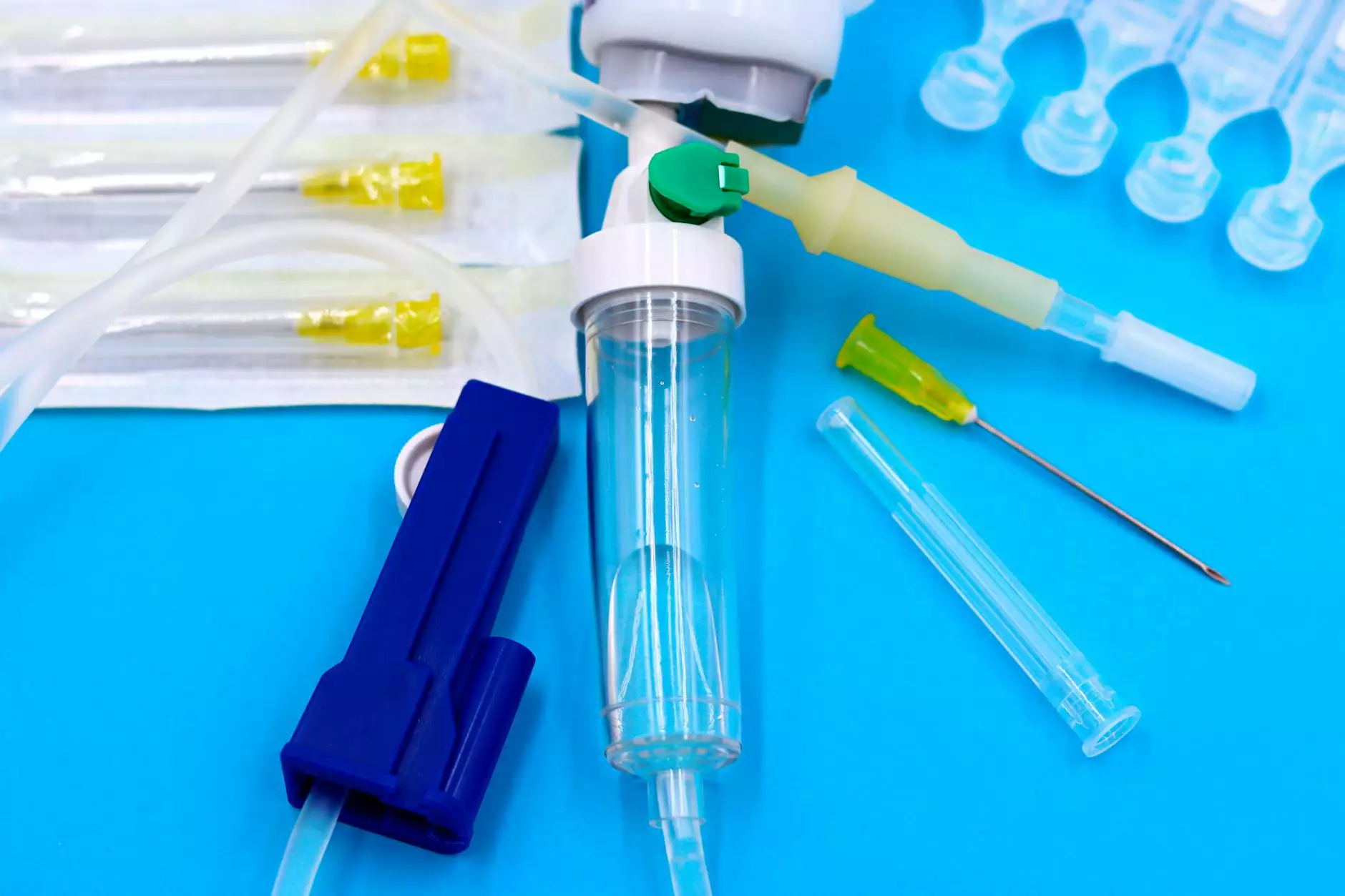
The process of mold plastic injection has revolutionized the manufacturing industry, offering unparalleled efficiency and precision in creating plastic components. In today’s fast-paced market, where the demand for high-quality products is ever-increasing, mastering this technique is essential for any manufacturer. This article delves into the nuances of mold plastic injection, highlights its applications, and explains why deepmould.net stands out as a leader in this domain.
What is Mold Plastic Injection?
Mold plastic injection is a manufacturing process that involves injecting molten plastic into a mold to create a solid object. This technique is widely utilized in producing a variety of plastic components used in consumer products, automotive parts, medical devices, and more. The process offers several advantages, including:
- High Efficiency: Once a mold is designed and built, it allows for rapid production with minimal material waste.
- Precision: The molds can be manufactured to very tight tolerances, ensuring that each piece is uniform in size and shape.
- Versatility: A wide range of materials can be used, including thermoplastics and thermosetting plastics, providing flexibility in design and application.
- Scalability: Ideal for producing both small and large quantities, making it suitable for various production runs.
The Process of Mold Plastic Injection
The mold plastic injection process can be broken down into several key steps:
1. Material Selection
The first step involves choosing the appropriate type of plastic material based on the desired properties of the finished product. Common materials include:
- Polypropylene (PP)
- Polyethylene (PE)
- Polyvinyl Chloride (PVC)
- Acrylonitrile Butadiene Styrene (ABS)
2. Mold Design and Fabrication
After material selection, the next critical step is the design and fabrication of the mold. Engineers use computer-aided design (CAD) software to create precise models of the mold that will shape the plastic. The following factors are considered during this phase:
- Mold geometry
- Cooling channels for efficient thermal management
- Ejection mechanisms for finished parts
3. Melting the Plastic
Once the mold is ready, the thermoplastic granules are heated until they melt. This stage requires precise temperature control to ensure the material achieves the right viscosity for easy injection.
4. Injection
The molten plastic is injected into the mold under high pressure, filling every cavity and ensuring a perfect fit. The speed and pressure during this phase are crucial for achieving optimal results.
5. Cooling and Ejection
After the injection, the plastic is allowed to cool and solidify within the mold. Once cooled, the mold opens, and the finished component is ejected. This step can involve additional mechanisms if complex shapes or features are needed.
6. Finishing Touches
Sometimes, additional processing is required, such as trimming, painting, or applying surface finishes, to achieve the desired final appearance and functionality of the component.
Applications of Mold Plastic Injection
Mold plastic injection is employed across a myriad of industries, showcasing its versatility and adaptability. Some notable applications include:
1. Automotive Industry
- Interior components such as dashboard panels and console trims
- Exterior parts including bumpers and grilles
- Functional components like clips, fasteners, and housing for electrical systems
2. Consumer Products
- Household goods ranging from storage containers to kitchen utensils
- Electronic devices, including casings and functional parts
- Toys and games, ensuring safety and durability
3. Medical Devices
- Disposable syringes and medical tubing
- Complex components for diagnostic equipment
- Protective casings for surgical instruments
Benefits of Choosing Mold Plastic Injection
The mold plastic injection process offers countless advantages that make it the preferred method for producing plastic parts:
1. Cost-Effective Production
While the initial investment in mold design and fabrication can be significant, the long-term benefits are substantial. Once the mold is established, the cost per unit decreases dramatically, especially for high-volume production runs.
2. Enhanced Product Quality
Injection molding allows for high precision and replicability in manufacturing. This process reduces production errors, leading to enhanced product quality and consistency, which is critical in competitive markets.
3. Design Flexibility
Mold plastic injection supports complex shapes, enabling companies to innovate and differentiate their products. This flexibility is vital in an era where branding and unique design can set a product apart from the competition.
4. Reduced Waste and Sustainable Practices
Efficient material usage and the ability to recycle excess plastic contribute to lower overall waste. This environmentally responsible approach aligns with the increasing consumer demand for sustainability.
Challenges in Mold Plastic Injection
Despite its many advantages, mold plastic injection is not without its challenges:
1. Initial Setup Costs
The upfront costs associated with mold creation can be a barrier for companies looking to adopt this process. However, businesses must weigh these costs against the potential for long-term savings.
2. Mold Maintenance
To ensure continued quality production, molds require routine maintenance and occasionally refurbishing to address wear and tear from repeated use.
3. Design Limitations
While mold plastic injection is highly versatile, certain design features may pose challenges, such as undercuts that complicate ejection without additional mechanisms.
Why Choose DeepMould.net for Mold Plastic Injection?
For businesses considering mold plastic injection, partnering with an experienced provider is crucial. DeepMould.net stands out in the field for several reasons:
1. Expertise and Experience
DeepMould.net boasts a skilled team with extensive experience in mold design and injection processes. Their expertise ensures high-quality results tailored to client specifications.
2. State-of-the-Art Technology
The company utilizes advanced technology and machinery that ensure precision and efficiency in every project, reducing production times without compromising quality.
3. Commitment to Sustainability
DeepMould.net emphasizes sustainable practices, using recyclable materials and efficient production techniques that resonate with environmentally conscious consumers.
4. Comprehensive Services
From initial design to final production, DeepMould.net offers end-to-end services that simplify the manufacturing process for clients, allowing them to focus on their core business.
Conclusion
In conclusion, understanding the intricacies of mold plastic injection is essential for businesses looking to remain competitive in the modern manufacturing landscape. This process not only provides efficiency and precision but also allows for innovative product design and sustainability. By partnering with industry leaders like DeepMould.net, companies can leverage expert knowledge and advanced technology to achieve superior results. Embrace the future of manufacturing with mold plastic injection and transform your production capabilities today!